Sponsored article
How do you look after deburring discs to ensure their longevity?
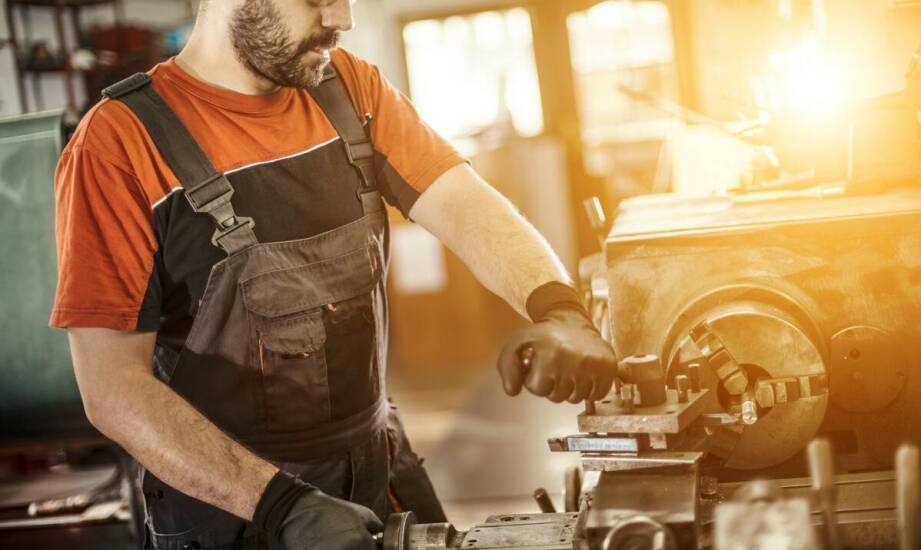
The care of deburring discs is crucial in machining processes, as it affects the efficiency and quality of the work. Proper maintenance can extend the life of these machines and improve deburring results. It is therefore worth learning about the methods of caring for them and the benefits of using them properly. Proper tool maintenance translates into better machining results, which is important for any company involved in the process.
Read more: What quality standards should road transport packaging meet?
Basic maintenance principles
Basic maintenance includes regular cleaning and lubrication of tools. These operations should be carried out in accordance with the manufacturer ’s recommendations and at a frequency depending on the intensity of use. Taking care of deburring tools affects their performance and reliability, resulting in better work results. It is also worth looking at the range of companies such as Madora, which offers high-quality products and support in the maintenance and operation of these devices.
Read more: The most important features of impulse sealing
Cleaning methods for deburring discs
Cleaning methods for deburring discs include a variety of techniques, both manual and with specialised chemicals. For simple dirt, brushes or rags soaked in suitable preparations can be used. When dirt is more difficult to remove, it is worth reaching for the dedicated chemicals available on the market. When choosing a cleaning method, the type of equipment and the characteristics of the contamination should be taken into account. Thanks to this, you can effectively remove dirt and protect components from damage, which will contribute to their longer service life.
Tool lubrication
Lubrication of deburring discs is crucial to the longevity of their operation. When choosing the right lubricants, it is worth paying attention to the manufacturers’ recommendations and the specifics of the equipment used. Application techniques also make a difference – grease should be applied evenly and in the right amounts to avoid over- or under-application. This optimises the reduction of friction and wear, resulting in a longer service life and better quality of operations. Regularly checking the lubrication status is another step in looking after your equipment.